Laiwu Iron and Steel's 12000m3 / h air separation unit is a complete set of technical equipment imported from the German Linde company, using air low temperature rectification method to produce high-purity oxygen, nitrogen and argon. The brief production process is as follows: the raw material air is compressed and pre-cooled, and the moisture and CO2 are removed at the molecular sieve station. After entering the cold box, it is divided into two strands, one is cooled by the main heat exchanger countercurrent to the high pressure tower, and the other is expanded. Cool down and enter the low-pressure tower. The air undergoes two stages of rectification in the high-pressure tower and the low-pressure tower, and gas nitrogen and liquid nitrogen are separated at the top of the low-pressure tower, and liquid oxygen is separated at the bottom. An argon-rich argon fraction (about 90% O2, 10% Ar, and 0.05% N2) is drawn in the middle of the low-pressure column, sent to the primary crude argon column to remove oxygen, and gaseous argon is drawn from the top of the primary crude argon column (purity about 99.8 %) Sent to the bottom of the secondary crude argon column to further remove oxygen. Finally, argon with an oxygen content of less than 0.0001% is sent to a pure argon column to remove nitrogen and hydrocarbons to produce pure argon.
1 Control system structure
The air separation plant adopts the INFI-90 control system of Elsag Company of Canada, in which INFI-90DCS is used as the process control system to complete data collection, loop regulation and logic sequence control; DECAlpha200 computer is used for automatic variable load control (ALC). In order to ensure the safe and reliable operation of large-scale equipment, 5 PLCs were selected on site to complete the local control of air compressor, nitrogen compressor, oxygen compressor and two expansion turbines. The main control room is equipped with an engineer workstation, an operator monitoring station, an automatic variable load process station and three printers for production process monitoring, software configuration and graphics, alarm printing. The network structure of the control system is shown in Figure 1.
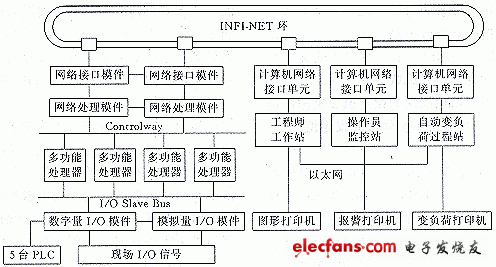
Figure 1 Schematic diagram of the control system network structure
The biggest feature of the system configuration is the redundancy function, including:
The dual ring thermal redundancy of the INFI-NET ring.
The two network interface modules are hardwired to be redundant with each other to ensure uninterrupted data on the ring network.
The four multi-function processors are respectively configured into two pairs of mutually redundant modules with hard wires to ensure uninterrupted execution of system programs.
The engineer workstation and operator monitoring station are configured redundantly via Ethernet and share two printers.
2 Control functions
2.1 DCS process control
ElsagDCS mainly completes the data collection and loop control of product processing area and storage area. The control circuit mainly has the flow control of the air suction of the air compressor; the liquid level control of the air cooling tower and the water cooling tower; the operation steps and switching control of the two molecular sieves; the pressure, flow and temperature control of the rectification towers and pipes in the cold box; Liquid level and pressure control in storage tanks, etc.
In order to make the whole production process run stably, there is a cascade control between each circuit. The air separation unit mainly produces oxygen, and the oxygen flow adjustment circuit is shown in FIG. 2.
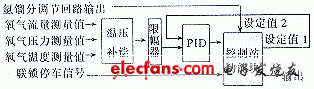
Figure 2 Schematic diagram of the oxygen flow adjustment loop configuration
Since the adjustment of oxygen flow rate will affect the changes of argon fraction, oxygen pressure, and oxygen temperature, the interlock stop signal will make the loop in a safe setting state, so these factors need to be considered in the design process to make it in a cascade state , To ensure the safe regulation of oxygen flow.
Laiwu Iron and Steel's 12000m3 / h air separation unit is a complete set of technical equipment imported from the German Linde company, using air low temperature rectification method to produce high-purity oxygen, nitrogen and argon. The brief production process is as follows: the raw material air is compressed and pre-cooled, and the moisture and CO2 are removed at the molecular sieve station. After entering the cold box, it is divided into two strands, one is cooled by the main heat exchanger countercurrent to the high pressure tower, and the other is expanded. Cool down and enter the low-pressure tower. The air undergoes two stages of rectification in the high-pressure tower and the low-pressure tower, and gas nitrogen and liquid nitrogen are separated at the top of the low-pressure tower, and liquid oxygen is separated at the bottom. An argon-rich argon fraction (about 90% O2, 10% Ar, and 0.05% N2) is drawn in the middle of the low-pressure column, sent to the primary crude argon column to remove oxygen, and gaseous argon is drawn from the top of the primary crude argon column (purity about 99.8 %) Sent to the bottom of the secondary crude argon column to further remove oxygen. Finally, argon with an oxygen content of less than 0.0001% is sent to a pure argon column to remove nitrogen and hydrocarbons to produce pure argon.
12000W Three Phase AC Source System
APM model SPS300VAC12000W 3 phase AC Power Supply system is ideal for every test scenario: like home electronic appliances, power adapters, LEDs, and even laboratory testing etc. This ac source system is single 3-phase output programmable AC power supply which provides with high power density.
Some features as below:
- 5.6`` large touch color screen, possess complete functions and easy to operate.
- Support for USB data import/export and screen snap from front panel.
- AC+DC mixed or independent output mode for voltage DC offset simulation.
- Capable of setting voltage and current output restriction, support for constant current output mode.
- Capable of setting output slope of voltage and frequency.
- Capable of setting ON/OFF phase angle.
- With reverse current protection to avoid current flowing backward.
- Built-in power meter, which is capable of measuring 5 electrical parameters per phase, including voltage, current, power, etc.
- Support mA current measurement function.
10800W Three Phase AC Source System,Uninterruptible Power Source,Three Phase Generator,3 Phase Power Converter
APM Technologies Ltd , https://www.apmpowersupply.com