First, the maintenance principle
1. Always check for oil leaks before starting each time. Inspect critical areas such as oil pipes, control valves, fuel tank, and small piston. Ensure all bolts are securely fastened and that electrical connections are intact. Regularly inspect and maintain the integrity of all components.
2. Allow a warm-up period of at least 15 minutes before use.
3. Lower the piston to its lowest position after completing each test.
4. Clean up any debris after shutdown and perform anti-rust treatment on the testing table.
5. After prolonged operation, perform necessary inspections and maintenance. Apply molybdenum disulfide grease to steel plates weekly, lubricate screws twice a month, and check chain tightness every six months, applying extreme pressure molybdenum grease. Regularly apply lubricating oil to sliding parts and anti-rust oil to rust-prone areas to keep the equipment clean and protected.
6. Avoid exposure to high temperatures, excessive humidity, dust, corrosive substances, or water, which can damage the instrument.
7. Replace hydraulic oil after 2000 hours of operation or cumulative usage.
8. Conduct annual inspections to ensure everything remains in good working condition.
9. Keep a record of all operations and maintenance activities.
10. Follow the startup sequence specified in the "Material Practices for Material Testing Machines." After turning on the equipment, allow it to warm up for 15 minutes. Once the electrical signal stabilizes, proceed with the test.
Second, the computer part
11. Do not install additional software on the computer, as this may interfere with the proper functioning of the testing machine's operating software.
12. Before starting the machine, verify that all connection cables between the computer and the host, as well as power plugs and sockets, are correctly connected and secure. Only start the system if everything is properly connected.
13. Protect the computer from virus infections by using reliable antivirus software and avoiding suspicious downloads.
Third, the test part
1. After starting the machine, allow it to preheat for 15 minutes. Test only after the equipment has stabilized.
2. If the power was just turned off, wait at least 10 seconds before restarting to avoid damaging internal components.
3. Never plug or unplug power cords or signal cables during operation, as this can easily damage control components.
4. During the test, avoid pressing buttons on the hydraulic panel, operation box, or test software to prevent interference with the process.
5. Do not touch the device or cables during testing to maintain data accuracy.
6. Select the appropriate fixture based on the test conditions to prevent damage to the fixture.
7. In case of a power outage, immediately turn off the power and wait until the supply is stable before restarting. Frequent power switching can damage internal components or the computer.
8. The operator should remain near the equipment while it is running. If leaving, always turn off the machine.
9. Regular maintenance is essential to protect the equipment from high temperature, humidity, dust, and corrosive elements.
10. Do not force test irregular samples, as this can damage the equipment.
Fourth, host maintenance
1. Fixtures should be coated with anti-rust oil for protection.
2. Avoid placing heavy or hard objects on the test bench surface to prevent damage.
3. Clean the equipment thoroughly after each test.
4. Apply a layer of molybdenum disulfide extreme pressure grease (MoS2) to the sliding surfaces of the steel plate and lining plate weekly.
5. Check the screws of the jaws before each test. Tighten them if loose.
6. Regularly check the tension of the sprocket. If loose, adjust the tensioner accordingly.
7. All moving parts should be lubricated regularly. For example, the chain and lead screw can be coated with MoS2 grease, and the test bench surface should be treated with anti-rust oil.
8. Before each test, check whether the large nut connecting the light bar and the screw is loose. If so, remove the top wire and tighten it carefully. Avoid over-tightening to ensure smooth rotation—typically, you can loosen it by about a quarter turn after tightening.
Fifth, hydraulic system maintenance
1. When not in use for an extended period, disconnect the main unit’s power. If the device is in standby mode, ensure the transfer switch is in the “loading†position. Leaving it in the “fast reverse†position will cause the electromagnetic reversing valve to stay energized, reducing component lifespan.
2. Regularly inspect the hydraulic system for oil leaks. Load the equipment to 80% of its full scale and hold for 10 minutes. If oil leakage is detected, replace the affected hydraulic components and seals.
3. Monitor the oil level in the tank (check the cursor on the hydraulic source). If the oil level drops below 3/4 of the mark, refill the hydraulic oil to the top of the cursor.
4. Hydraulic oil viscosity changes over time due to usage and aging. Replace the oil and filter element after 2000 hours of operation or cumulative use. Drain the old oil first, then clean the tank with kerosene before refilling.
5. Always filter the air when re-energizing to ensure clean hydraulic oil, which is essential for the system’s performance.
6. Replace the entire hydraulic system’s seal assembly periodically. It is recommended to replace moving part seals every three years and joint seals annually.
7. Verify the temperature relay setting. The factory setting activates the radiator when the oil temperature reaches 40°C.
Sixth, control system maintenance
1. Regularly check the DCS controller’s wiring for secure connections. Tighten any loose connections promptly.
2. Turn off the DCS controller and computer if the equipment will not be used for an extended period.
3. Confirm that the control system, indicators, buttons, operation boxes, and fixtures are all functioning properly before beginning any test.
Shangyu Star Equipment Co., Ltd.
Located in Daoxu Town, Shangyu District, Shaoxing City, Zhejiang Province, the company specializes in production, product development, processing, and trade. Its main products include drying ovens, incubators, laboratory muffle furnaces, distilled water systems, clean workbenches, wind showers, fume hoods, and biological safety cabinets, among other complete purification equipment.
The company boasts a strong R&D team and a solid after-sales service system, positioning itself as a leader in China's laboratory equipment manufacturing industry. We welcome all customers to choose our products.
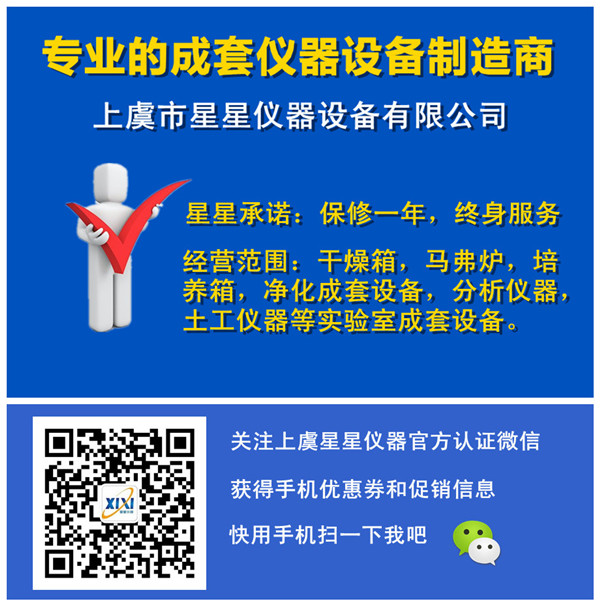
solar panel system
Solar Energy System,Solar Charging System,Evacuated Solar System,Solar System Product
JIANGSU BEST ENERGY CO.,LTD , https://www.bestenergy-group.com